Inventory management is a complex yet crucial process in running a business both productively and efficiently. But what is it exactly? And what is the right inventory management system for you?
Managing inventory and stock levels requires a high degree of accuracy. If not done properly, it can cause a few headaches along the way.
Any mistakes or miscounting can result in inadequate stocks, unnecessary purchases, and delayed shipments, which can have a negative impact on your company’s operations.
In this respect, inventory management systems can act as a perfect tool, helping you optimise your stock levels and keep everything ticking as it should.
But how do inventory management systems work, and what benefits do they bring? Let’s take a look!
Don’t forget that if you’re on the hunt for additional storage space, Cleveland Containers has a wide range of shipping containers that will help you keep your products and equipment safe and well-organised all year long.
If you have any questions, feel free to get in touch – we’re always on hand to give you guidance and support.
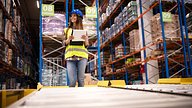
Understanding Inventory Management Systems
What is an inventory management system?
In short, an inventory management system is a piece of software that’s used to track and monitor inventory items in an organisation, allowing you to always keep an eye on stock levels and stock content.
The goal of an inventory management system is very simple: ensure that the right items and products are available at the right time and in the right quantity.
Having everything in place when you need it can have a hugely positive impact on your day-to-day activities, giving you the chance to operate as effectively and productively as possible.
Features of effective systems
Stock management systems come with a wide range of handy features. Based on your business’s needs and operations, you may want to opt for a system that includes some (or all) of the following tools:
- Real-time tracking – With real-time tracking, an inventory management system can provide you with up-to-date information on stock levels and numbers. This will give you a clear, full picture of your inventory situation at any given time.
- Ordering management – This feature regulates and facilitates the processing of purchase orders, sales orders, and so on. This way, you can replenish your stock levels as and when required.
- Analytics and reporting – Analytics and reporting are another very useful function. By providing you with inventory-based data, these features allow you to identify specific trends and make data-driven decisions when stocking up on products.
- Inventory forecasting – Inventory forecasting can be used to predict demand based on past sales data, allowing you to plan for upcoming stock requirements as necessary.
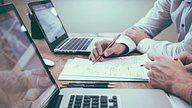
Types of Inventory Management Systems
Just about every business needs to keep an eye on their stock and inventory situation.
Generally, there are two ways to do this – manually or by using an automated system. Which one suits you and your company best?
Manual vs automated
Manual inventory management systems rely on pen, paper, and spreadsheets to keep all inventory information up to date. This means that your team will have to do all this by hand.
Manual options make a good inventory management system for small businesses with limited stock, as you can easily take note of your product levels as items come and go. However, it’s worth bearing in mind that this type of system is subject to human error, lacks real-time monitoring, and is a more time-consuming process overall.
On the other hand, automated stock management systems make full use of software and tech tools to keep count of inventory levels, boasting most (or all) of the features mentioned above.
With an automated system, you can ensure that nothing slips through the cracks while benefiting from real-time visibility, accuracy, and efficiency.
Specialised industry systems
Of course, based on the industry you operate in, you may need to rely on specialised systems to keep everything in check.
For example, businesses in the catering and hospitality sector might require an extra feature that monitors perishable items and keeps track of expiry dates. This can prevent both avoidable waste and financial losses. If you’re in the food and beverage industry, you really should check out our catering shipping containers. Built to your requirements, these units can include features such as shelving, partition walls and ventilation. Refrigerated containers could also be a good option if you’re storing/ shipping cold goods.
As for the manufacturing industry, it’s wise for companies to be aware of material levels at all times. In fact, any raw material shortage can impact their production process, halt their operations, and ultimately affect their productivity. Looking to improve your storage solutions on your site? Our shipping containers for the construction, engineering and manufacturing industries are durable and secure, so can be used for storing everything from stock to tools and machinery.
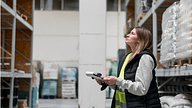
Benefits of a Complete Inventory System
As well as offering you a comprehensive idea of what your stock levels look like, inventory management systems come with plenty more advantages.
For instance, some of its most noticeable benefits include:
- Improved accuracy – Real-time data and information help reduce the risk of mistakes and avoid unnecessary issues such as overstocking, stockouts, or general stocking errors. With up-to-date stats at hand, you can make more informed and accurate decisions.
- Enhanced efficiency – By eliminating the risk of mistakes and cutting on time-consuming tasks, such as manually reviewing your stock levels (especially in the case of big companies), you can increase your business’s efficiency. This allows you and your people to focus on other important activities, maximising both your time and energy.
- Cost savings – Inventory management systems give you the chance to predict demand and optimise stock levels. By preventing mistakes such as under- or overstocking, you can keep your finances in check and save precious money.
Choosing the Right System for Your Business
If you’re set on investing in an inventory management system to aid your daily business operations, the first step is to always think carefully about your organisation’s requirements. How does your company function? What sector do you operate in?
Answering these questions will help you identify your priorities and select a system that ticks all the right boxes, meaning you can benefit from a handy tool to take your company to the next level.
As well as reviewing your business’s needs, consider things such as scalability and integration. If you plan or expect to grow in the near future, you may want to opt for a system that’s able to scale alongside your organisation.
This way, you can keep track of your increasing inventory volumes and ensure you’re prepared for additional sales channels.
If you’re looking to expand as a business and need extra storage room, shipping containers are a safe, reliable option. Thanks to their portable nature and standardised dimensions, they can be added, moved, and stacked as you please to suit all your organisational needs.
Browse our large collection of container units, and don’t forget that Cleveland Containers’ friendly team is always on hand to offer support and walk you through your best options.
Need our help?
Talk to us about your container project today...
You may also be interested in...
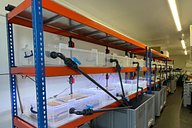
Managing Inventory with a Storage Container
Discover how storage containers can streamline your inventory and stock management systems, from stock control to optimising limited space.
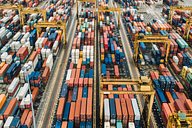
The Importance of Demand Forecasting in Supply Chain Management
Learn about the significance of demand forecasting in supply chain management with our insightful guide.
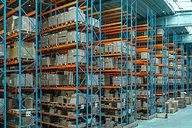
Supply Chain Planning & Management
Discover more about the ins and outs of supply chain management systems, learning how they can help you take your business to the next level.
0 Comment
Please leave a comment using the form below